Stand Up Pouch Manufacturing
101: How Stand-Up Pouches are
Made
The first stand-up pouch was manufactured via stand up pouch manufacturing in 1963. Originally two flat sheets were sealed together, but that basic design has gone through a series of improvements as companies pursue durability and aesthetics that make the packaging attractive to consumers.
Stand up pouches use fewer resources than conventional packaging such as boxes and cartons. They can also be highly personalized making them the truly modern way to package products.
These bags are air and watertight which makes them ideal for packaging food, chemicals, some types of clothing, etc. They also give companies an avenue to market their brands. That's why packaging suppliers are always coming up with new features to accommodate branding needs.
The latest features on these bags include zippers, spouts, and top holes that make pouring liquid or powder content less messy.
So how is a stand up pouch manufactured to achieve durability, functionality, and even preserve the environment? Read on to find out and email us to get started! Continue to learn more about what to expect from stand up pouch manufacturers.
The Process
Continue to read to learn more about the pouch manufacturing process. Stand up packaging bags are built from plastic composed of a resin of granular polyethylene. This composition makes it easy to melt and flatten into different shapes.
This material is then used to create a long polyethylene tube. This tube can be over a mile long, but the cloth used to make it has a width of less than a tenth of a millimeter. This tube is allowed to cool before being flattened by a series of rollers into a long strip of plastic. The strip is wound on a cylinder to form a sheet.
Each bag has several films with each one made with materials that play into the water-proof and airtight features of the bag. Manufacturers select the materials carefully to ensure the packs are also durable.
The innermost layer keeps the content quality intact. It also comes into direct contact with the pack's content. Therefore, it is made of the polymer LLDPE which is FDA-approved.
The outermost layer often bears the company name and other branding messages. Manufacturers use alcohol-based ink to print words and images on these packs.
When the middle layer material is not made of clear material, it serves as a protective and branding layer. To achieve this, manufacturers opt for aluminum or films infused with metal or resin. Some companies choose kraft paper material for the outermost layer because it looks natural. Kraft material is also durable and has a texture designed to make branding easy.
These layers are then cut into different sizes and shapes then stuck together through sealing by applying heat. A large conversion machine receives the finished film roll. The film is cut into various parts as it goes through the system, forming the top part, rear, and underside of the stand up pouch.
Gussets are the bottom part and the reason a stand up pouch can stand. Part of the material used to make the rest of the bag goes through a machine that folds a perfect W-shaped gusset.
Functionality features are added separately depending on the pack. For example, spaces for handles are created through cutting with stamps. Zip locks are bound to the pack through heat. Perforations indicating where to cut are also added at the last bit in the process.
The layers must be cured in a special high-temperature drying chamber after the lamination process. If laminated films are not properly cured, they can peel apart days or weeks after the bags are completed. Drying takes 2–4 days, and regardless of the deadline, this part cannot be rushed.
However, not all stand up packs are of good quality. Like with every other products, the cheaper they are, the poorer their quality.
In the United States, stand up bags use is rapidly on the rise. Traditional packaging techniques, which are bulkier, more expensive to manufacture, less consumer-friendly, and consume a lot of resources, are rapidly being replaced by these bags.
Printing Pouches
There are many kinds of stand-up bags such as, shaped, spouted, liquid, printed, box, retort, foil barrier, inverted, wicket, frangible seal, multi-compartment, EZ-stand and reclosable pouch which breaks into the zipper, hook & loop, slider, and press-to-close categories.
All of them go through different kinds of printing depending on market needs. The following printing methods are widely used to print logos, names, and other aesthetics on stand-up bags.
Plate Printing
The most economic and versatile way to print stand up pouches is with Rotogravure plate printing. Thus, most stand-up bags go through plate printing to add the desired look and information of the top part. The printer has different cylinders which contain different colors that make up the entire design.
Plate printing offers a very wide color range. Digital printing uses direct surface printing ink which only uses cyan, magenta, and yellow, black and white. Moreover, with plate printing, you can play around with a mixture of gloss and matte.
Digital Printing
The ink used in digital printing does not permeate the substrate being printed on in many cases. It instead forms a thin layer on the substrate, which it adheres to further with UV curing or laser heating.
The main disadvantage of digital printing is that it is a more expensive method of printing on a basic level; as a result, digital printing is not recommended for long runs. Another significant limitation is its inability to match PMS colors. You can't have a mix of gloss and matte either. You can only go all matte or all gloss.
The digital printing method is not economically viable for big runs of up more than 5000 pieces. Multimillion-dollar firms may afford it but smaller firms are left to choose between the cost of buying raw materials and ordering attractive packaging.
If you're planning a high-color-count, a short-run project like trial runs, digitally printed stand-up bags are a good option. They are useful too when dealing with a constantly changing regulatory climate or have a lot of SKUs.
Flexography Printing
Loosely called flexo, flexography is a printing technique that employs a flexible (rather than a solid) plate. It's a more recent version of relief printing. Flexo printing is a popular method also used to print graphics, text, and images on stand-up pouches. Flexo printing is often used by a manufacturer on compostable bags to print directly on an outermost paper layer.
Get Your Custom Printed Stand Up Pouch Design Made Here
Now, you know more about the pouch manufacturing process. In a world where first impressions are everything, we'll help you step it up and get custom pouches for your products regardless of your industry. Contact us today to order samples and get an quick online quote. Email today! We're a top manufacturer in the country.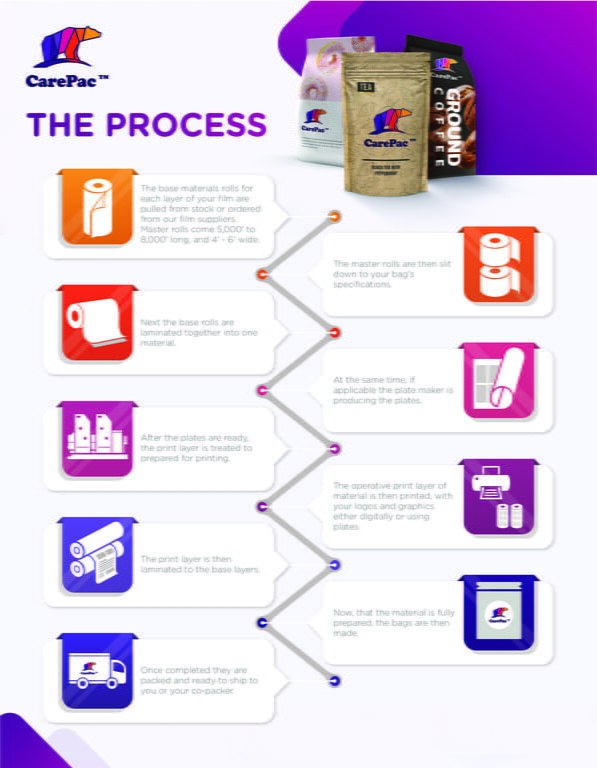
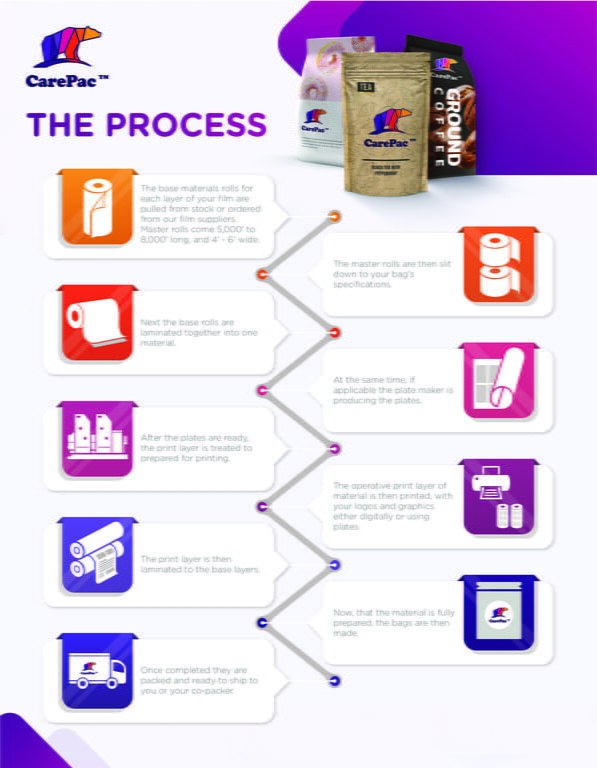